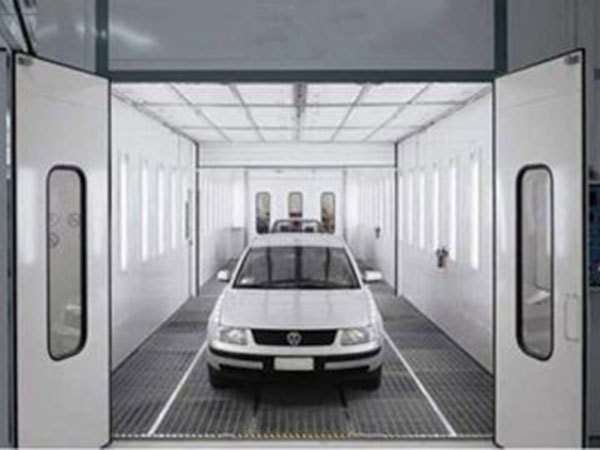
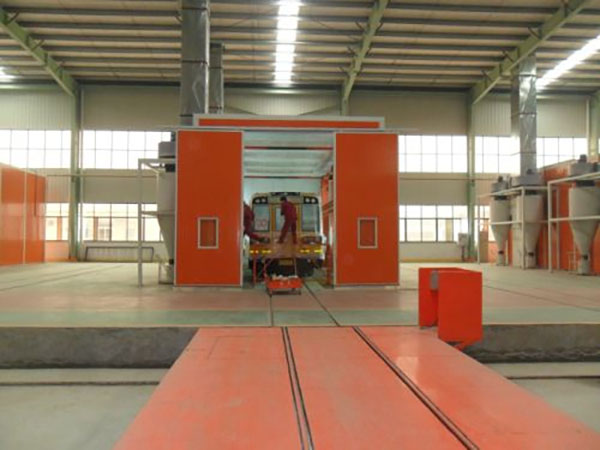
The paint room is composed of chamber body, lighting device, air filtration system, air supply system, exhaust system, paint mist treatment system, electric control system, safety protection device and so on.
Cleanliness is an important indicator to measure the quality of spray room, which is guaranteed by the air purification system. The air purification system of the spray room adopts ⅱ stage filtration, that is, the form of the combination of primary filtration (inlet filtration) and sub-efficient filtration (top filtration). The primary effect filter cotton is made of domestic high-quality non-woven cotton, made into bags, set in the fresh air outlet of the air supply unit, this filter form can reduce the wind resistance, increase the dust capacity, reduce the number of replacement; The top filter material is arranged at the bottom of the air supply duct and supported by the top mesh, which is high-quality C-type steel structure and treated with galvanization and rust prevention, with good stiffness, no rust and easy to replace the top cotton. The air supply filter layer in the chamber is precision sub-high efficiency filter cotton. The filter layer adopts the high quality and high efficiency filter cotton, with a large amount of flame retardant, let dust and high filtration efficiency, etc. The filter cotton for multilayer structure, of which the oily sandwich has a very high adhesion strength, to ensure clean air at dust quantity 100% more than 10 microns in diameter dust particle filter, dust particle diameter 3 to 10 microns dust concentration of not more than 100 / cm3, At the same time, the filter cotton can also play the role of air pressure. Main technical indexes of air filter cotton Filter cotton model thickness initial resistance final resistance capture rate dust capacity flame retardant capacity. Cc-550g 20mm 19Pa 250Pa 98% 419g/m² F-5 standard.The air supply system of spray room adopts up and down suction, which is mainly composed of air supply unit and air supply pipe. The air supply unit is arranged on the side of the chamber body. The air supply unit configuration (1 set of air supply unit) : The air supply unit is composed of fresh air inlet, primary filtering, air conditioning fan, electric damper and closed box. ◆ Initial effect filter: it is composed of profile filter frame and plate initial effect filter cotton, this kind of structure has low wind resistance and large dust capacity, the filter material is made of domestic high quality non-resistant cotton, which can effectively capture dust particles with diameters greater than 15μm. ◆ Blower: YDW double inlet air conditioning centrifugal fan with large air volume and low noise made by Yancheng with Siemens technology is selected. Rubber damping device is provided at the bottom of the fan. The spray chamber controls the load wind speed at 0.3m/s. The air supply is 32500m3/h. The main technical parameters of the fan are as follows: Machine number: YDW 4.0M0 Traffic: 10000 m3 / h Speed: 930 r/min The total pressure: 930 pa Power: 4KW/set Unit: 2 sets ◆ Fan base: the frame is welded with channel steel and Angle steel industrial profiles. The surrounding wall is made of 50mm rock wool board, which carries the weight and vibration of the fan and has good noise reduction effect. The fan base and exhaust fan base are assembled to facilitate disassembly and maintenance.It is mainly composed of exhaust fan, exhaust fan seat, exhaust pipe and air valve. Exhaust fan: The spray room is equipped with a set of exhaust units. The exhaust unit has a built-in 4-82 type centrifugal fan with low noise, large air volume, low energy consumption and high pressure head, which can discharge the exhaust gas processed by paint mist and dust adsorption and filtration into the air. Main technical parameters of selecting a single exhaust fan are as follows: Machine number: 4-82 7.1E Traffic: 22000 m3 / h Speed: 1400 r/min The total pressure: 1127 pa Power: 7.5Kw/ set Unit: 1 set Exhaust fan base: The frame is welded with channel steel and Angle steel industrial profiles, and the box body around is made of 50mm rock wool board, bearing the weight and working vibration of 1 exhaust fan and reducing noise. Exhaust pipe: 1.2mm high quality galvanized sheet and Q235-A Angle steel processing combination. Air valve: Manual air valve is set on the exhaust pipe to adjust the positive and negative indoor pressure.Dry treatment is adopted, that is, the first tile glass fiber filter felt is set at the lower part of the chamber body tunnel and supported by mesh frame; The second glass fiber filter felt is set at the outlet of the exhaust fan to ensure that the cleaning rate of paint mist reaches more than 95%, in line with GB16297-1996 "Comprehensive Emission standard of Air pollutants".
Under the exhaust fan is equipped with environmental protection box, strong absorption of organic matter. Dry treatment is adopted, that is, the harmful waste gas is adsorbed and purified by activated carbon, so that the waste gas after treatment meets the provisions of GB16297-1996 "Comprehensive Emission Standard of Air Pollutants". Activated carbon adsorption method is the use of activated carbon as adsorbent, the harmful substances in the gas on the large solid surface of activated carbon adsorption concentration, so as to achieve the purpose of purifying waste gas method. It has the advantages of high processing efficiency, solvent recycling, small investment and so on. The organic waste gas needs to be pretreated so as not to affect the adsorption capacity. Other specifications can be customized.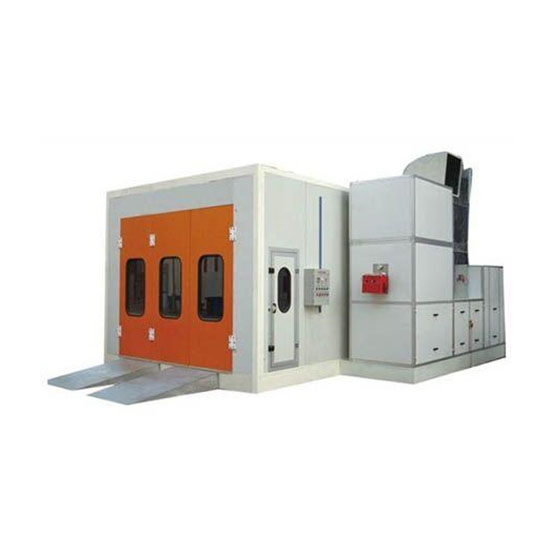
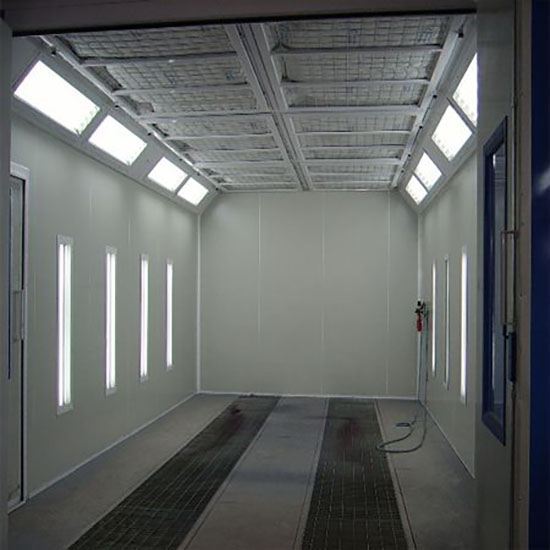